Injection Molding
RISU Plastic Group's Technology
Injection Molding
Injection molding is a forming technique suited to large-scale production of products with complex shapes. We use injection molding mainly for things like logistics industry materials, industrial components, medical related products, household products, commercial-use goods, and construction and engineering materials.
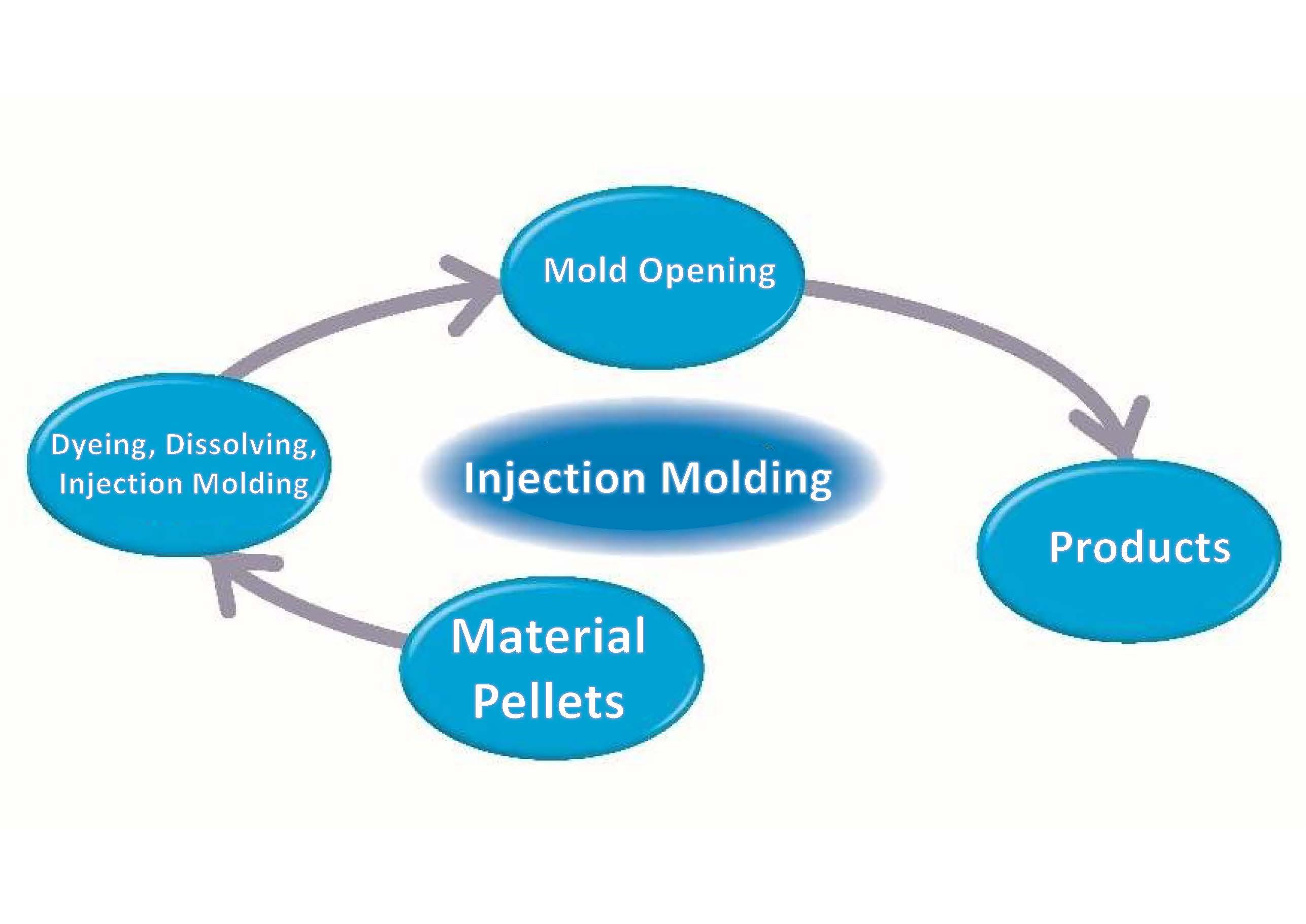
Molding Cycle
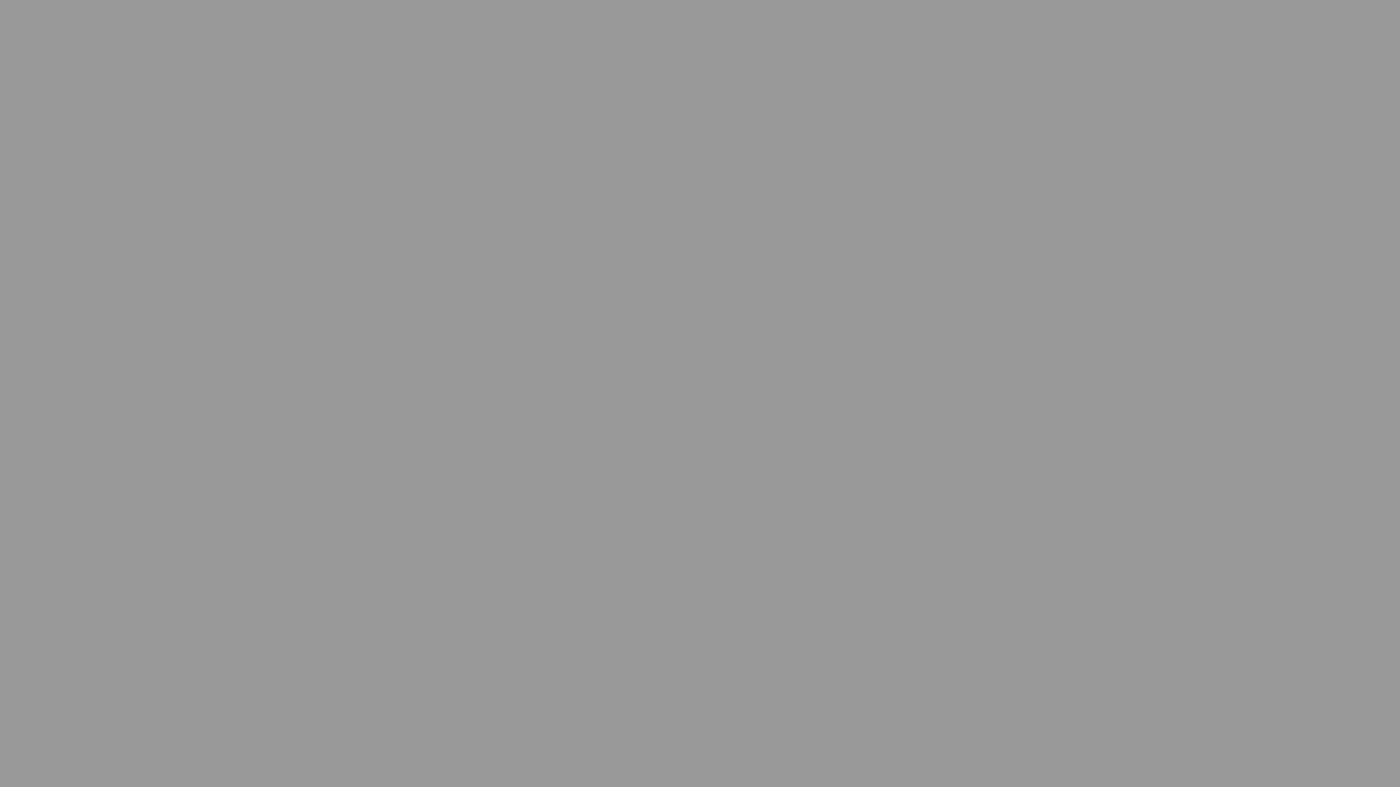
Inside the Mold
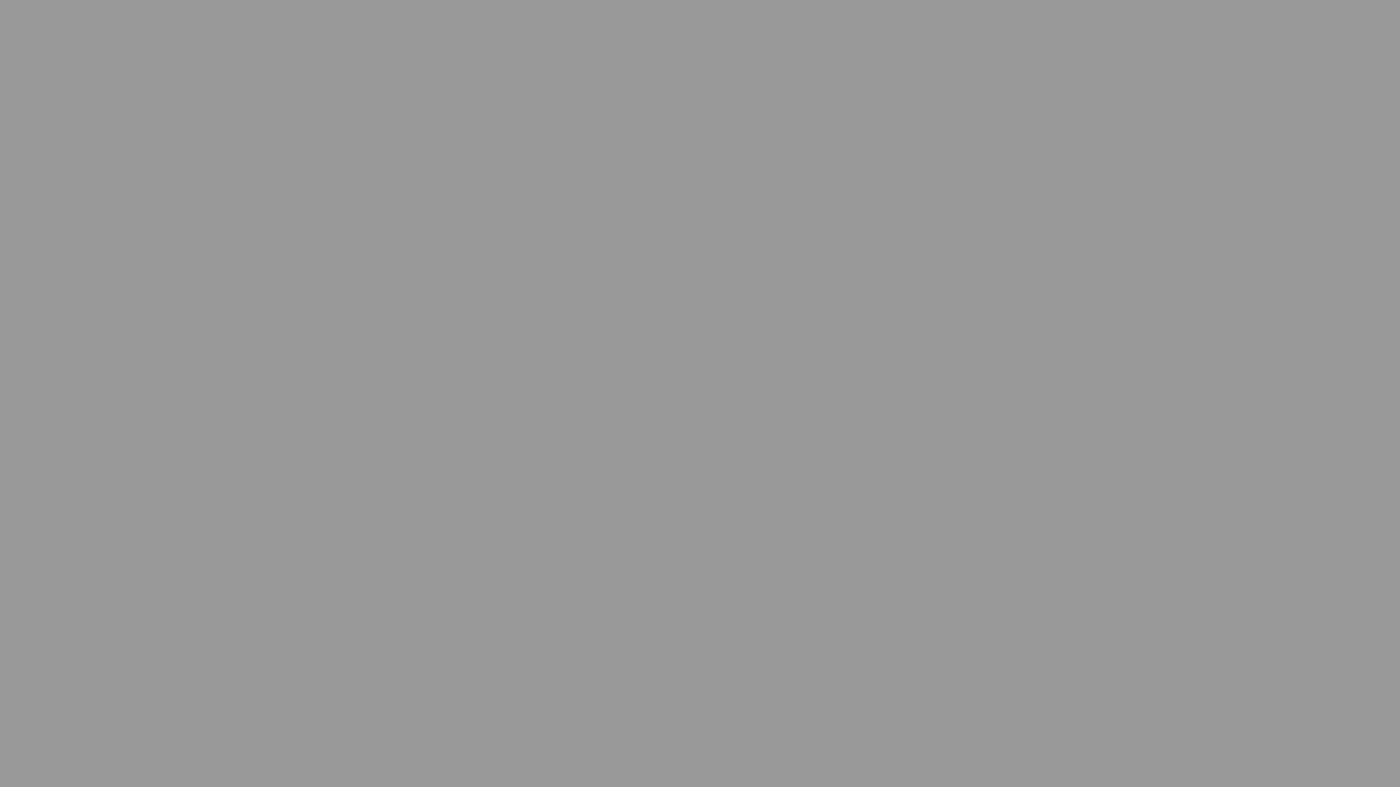
Finishing Process
The raw material is melted by electrically heating it to 150℃(320℉)-280℃(536℉) and then it is injected into the metal mold.
Once the material has cooled and set into shape, the metal mold automatically opens, and the product is lifted out by a robot and placed on a conveyor belt for finishing touches.
Forming Techniques
The forming method will depend on the function expected of the end product. We use the following forming techniques to produce products that cater to the requirements of our customers.
◆Two-Color Forming
Two-color forming is a technique used for molding the same material of two different colors, thereby producing products with striking designs. Unlike painting and hot stamping, two-color forming can create products with durable decoration and a sense of high quality. Different-material forming is a technique in which two types of material are adhered together during the forming process so as to produce an end product in which two different sets of properties co-exist. Because the need for latter processes such as adhesion work is eliminated, costs are brought down. These techniques also expand the applications of products.
<Two-Color Forming Products>
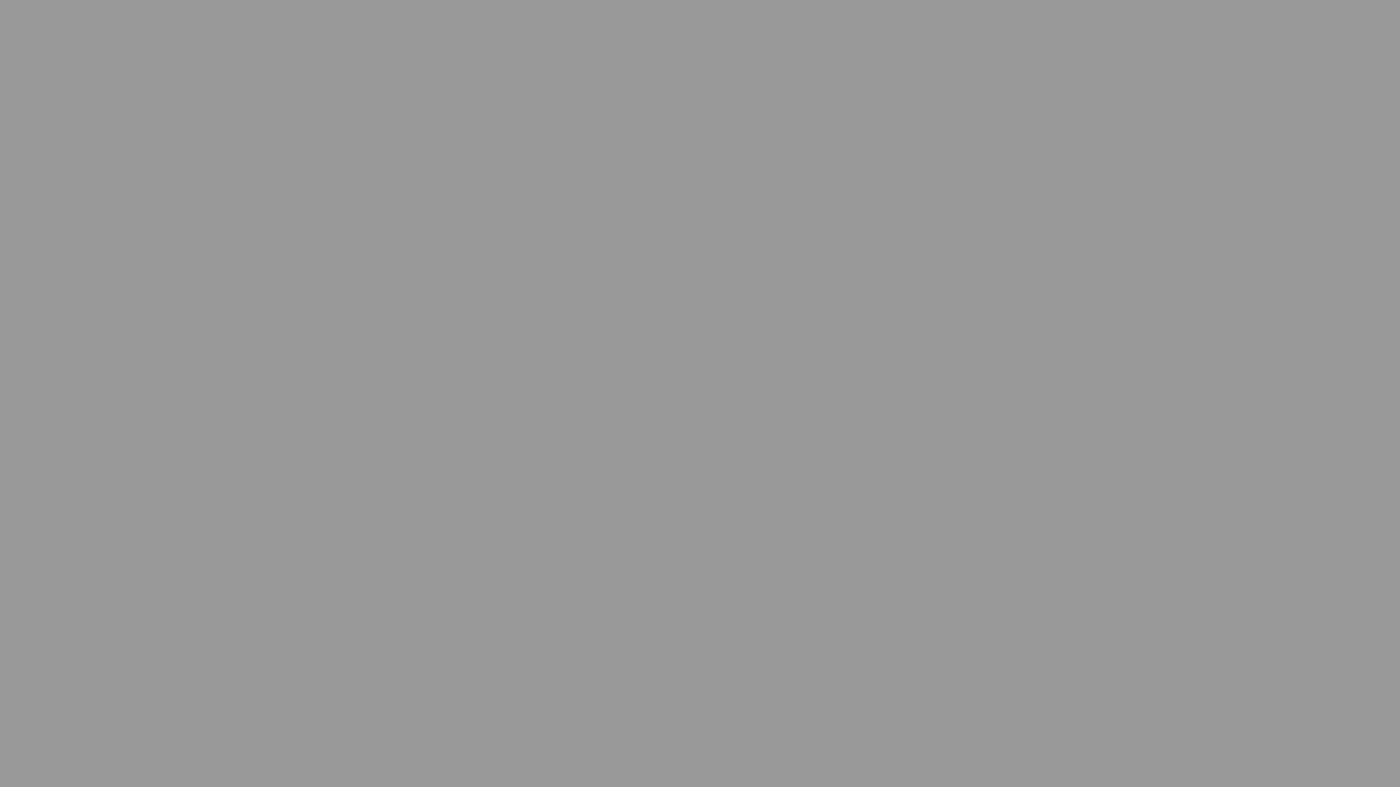
NF Container
<Product Utilizing Two-Color Core-Back>
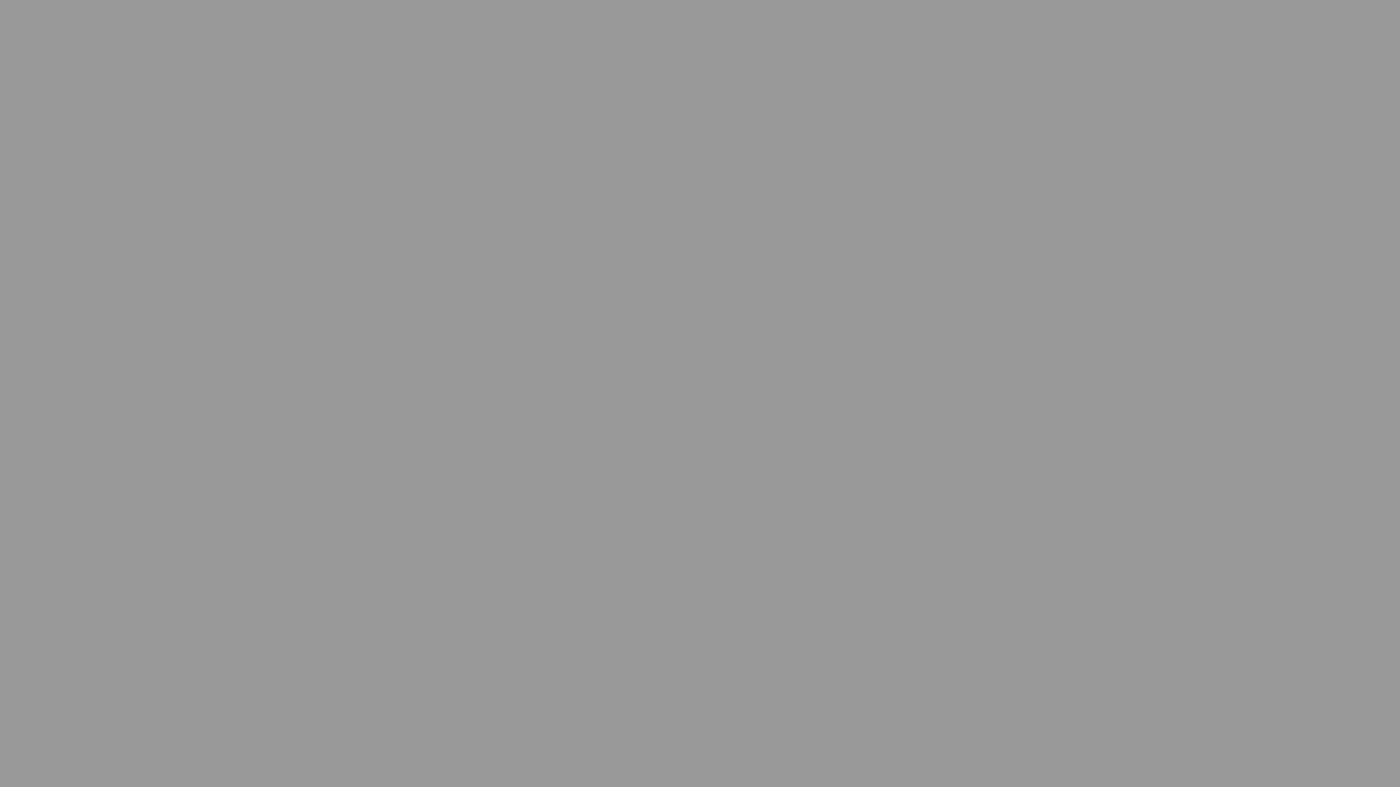
RISU BOX
◆Gas Injection
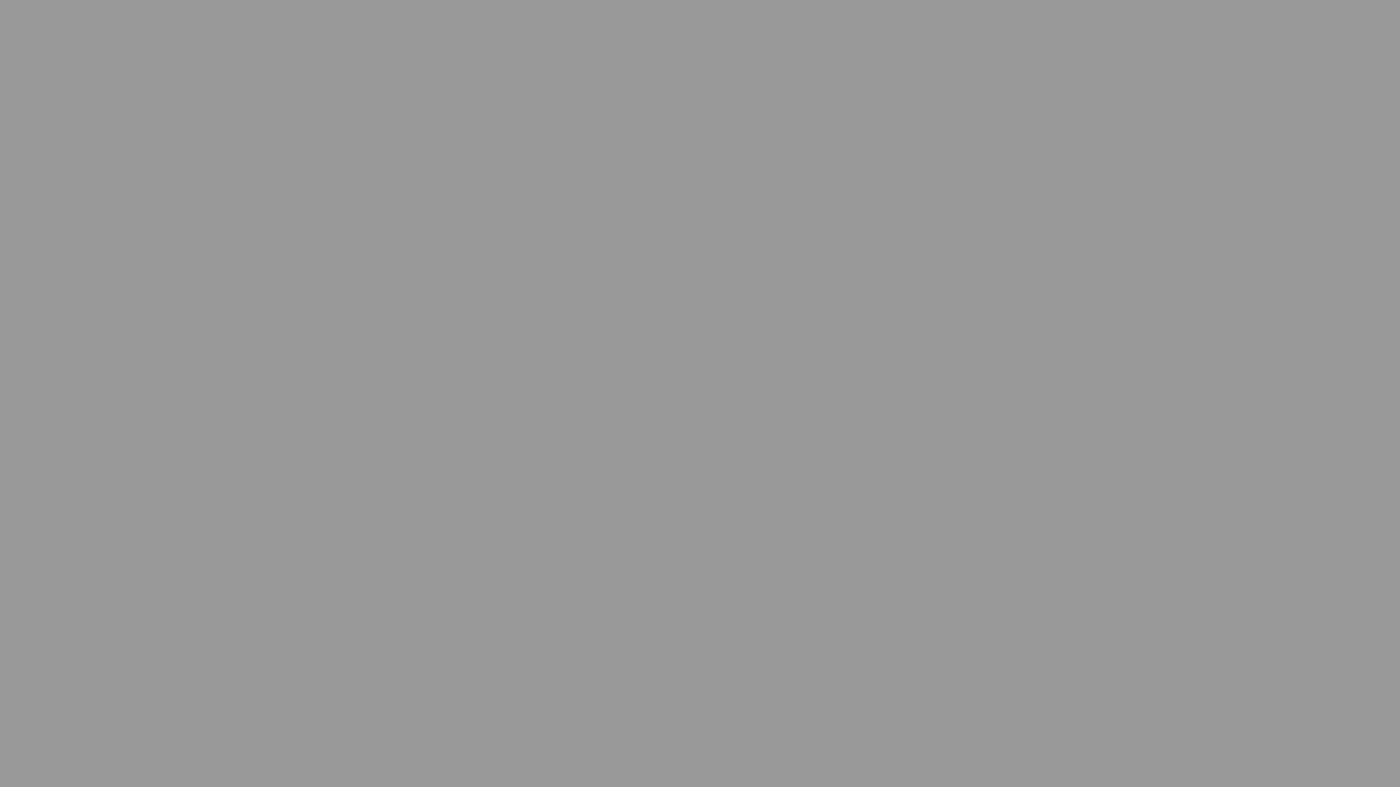
Our gas-injection technique involves injecting nitrogen gas into the thicker parts, thereby creating lighter weight and better structural strength while also preventing sagging and warping.
This method is adopted, for instance, to create a circular handle for a bucket.
◆Press Forming
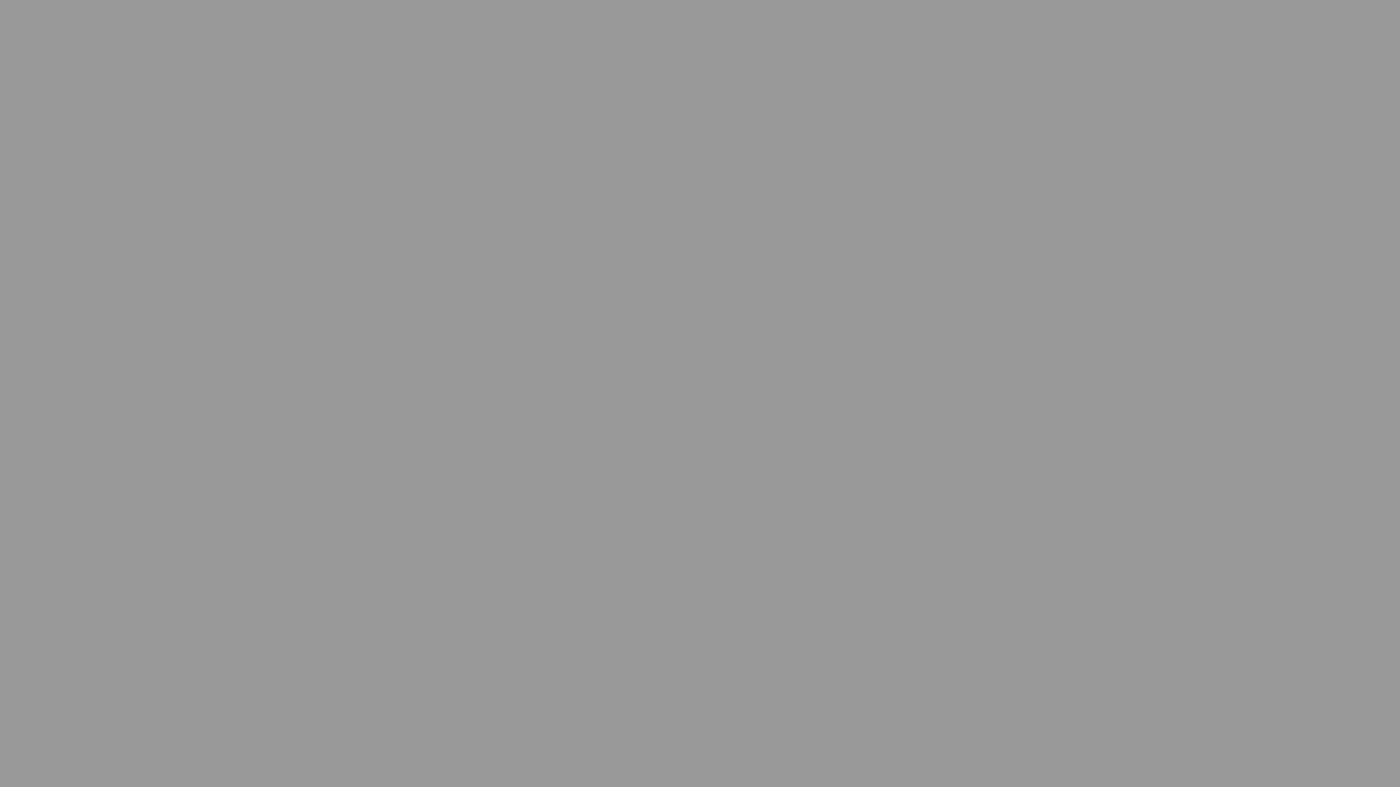
Press forming is a technique that involves opening a metal mold and running resin into the widened-out fluid passage without excessive pressure.
Because the material can be molded at low pressure, it is possible to create finished products with minimal warping. In addition, the spreading caused by pressing at the same time, makes the flow distance much greater compared to general injection forming.
For this reason, it is possible to form products with a larger projected area using molding machines with low clamping power.
Design assistance
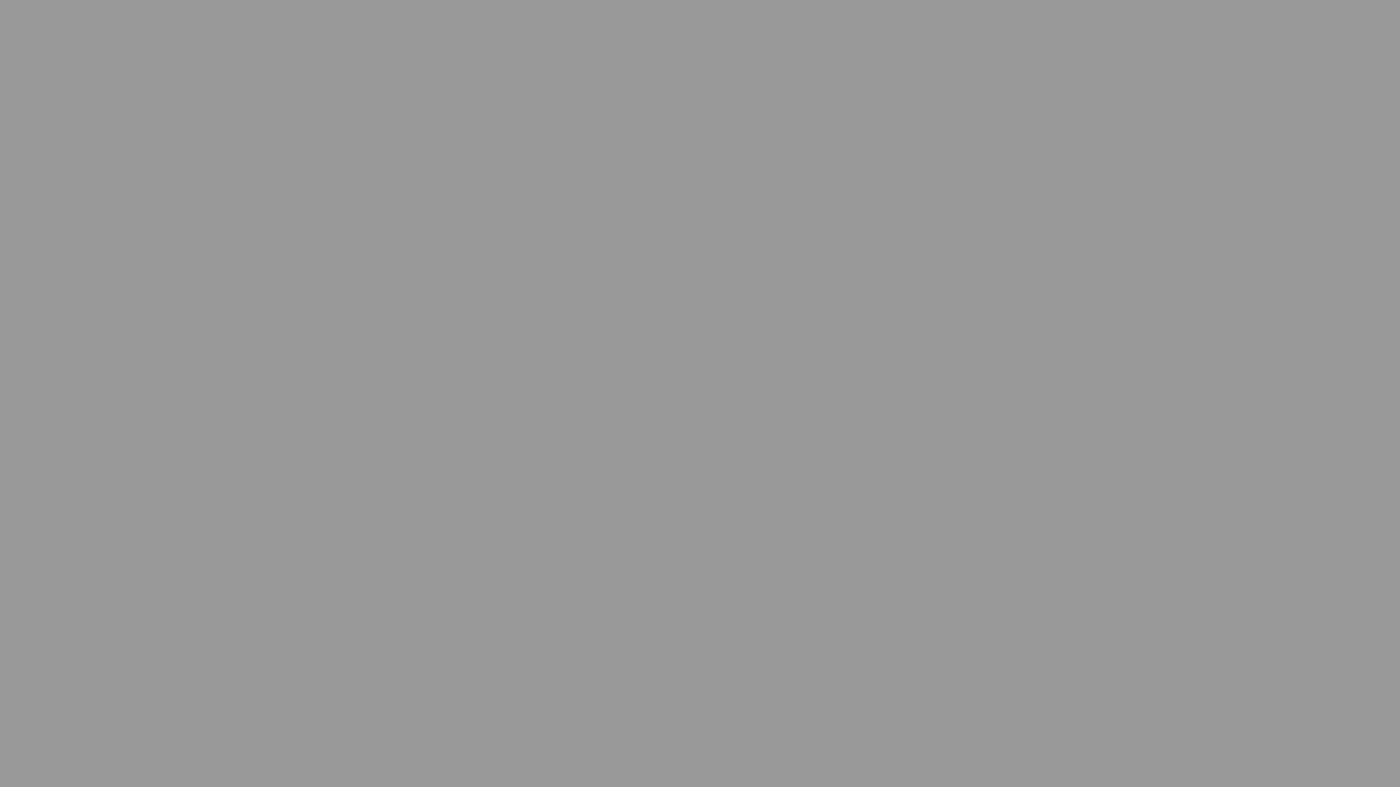
Design with 3-D CAD
Product design is conducted using 3D CAD, and by utilizing the CAD data for product development(CAE, 3D printer), design errors are eliminated.
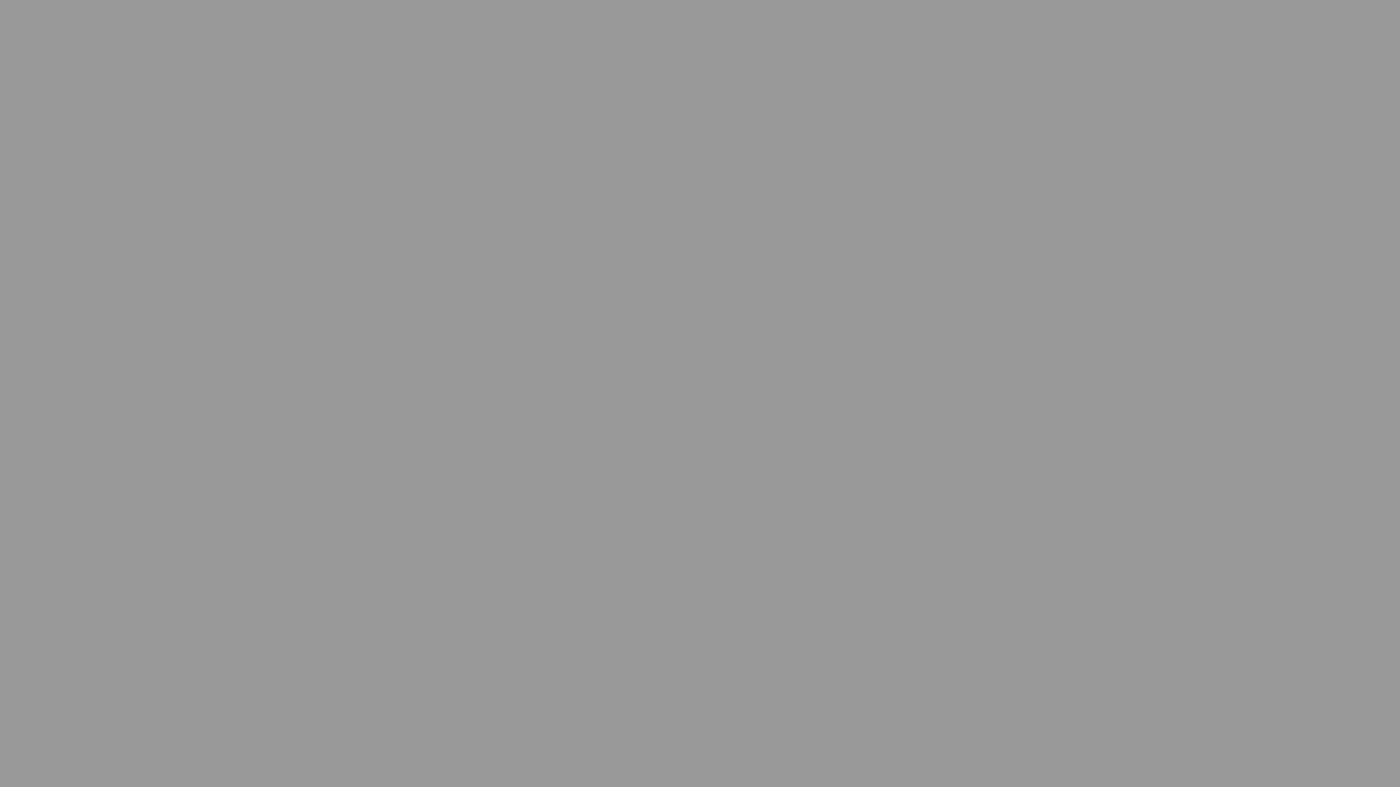
Design validation through CAE
By using structural analysis, we achieve designs that meet the required properties with lighter weight. Additionally, fluid analysis helps eliminate molding issues after mold production, leading to enhanced quality, cost reduction, and shortened lead times.
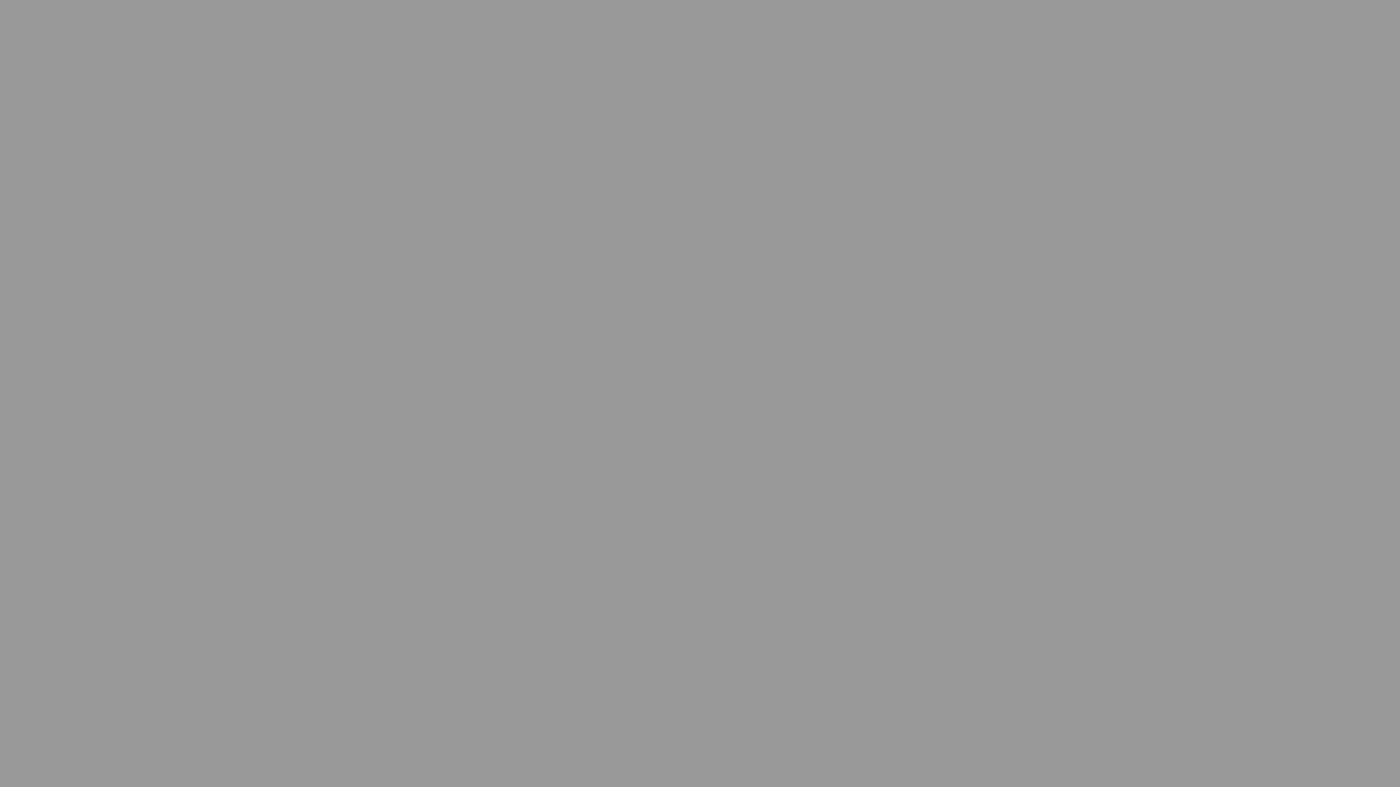
Shape sharing via 3D printers
Confirming the shape with models ensures alignment of understanding wigh custmers, allowing for accurate integration of their need s into the product.